Hudson Yards, the mega-development reshaping Manhattan’s Far West Side, needs little introduction; it has been both praised and vilified for its gigantic scale and contentious urban ethos. Regardless of the controversy surrounding it, the project showcases some ambitious engineering. Designed by Diller Scofidio + Renfro (DS+R) with Rockwell Group, The Bloomberg Building’s versatile ETFE cladding and mobile shell exemplify the development’s remarkable construction.
The Bloomberg Building, home of The Shed, a cultural center, is a multipurpose structure composed of four stories of loftlike spaces clad in a unitized glass curtain wall. The building is encased in a pillowy shell of diamond-shaped ETFE panels that rest on six gargantuan tracked wheels—bearing some resemblance to the industrial shipping infrastructure formerly located on the nearby Hudson River.
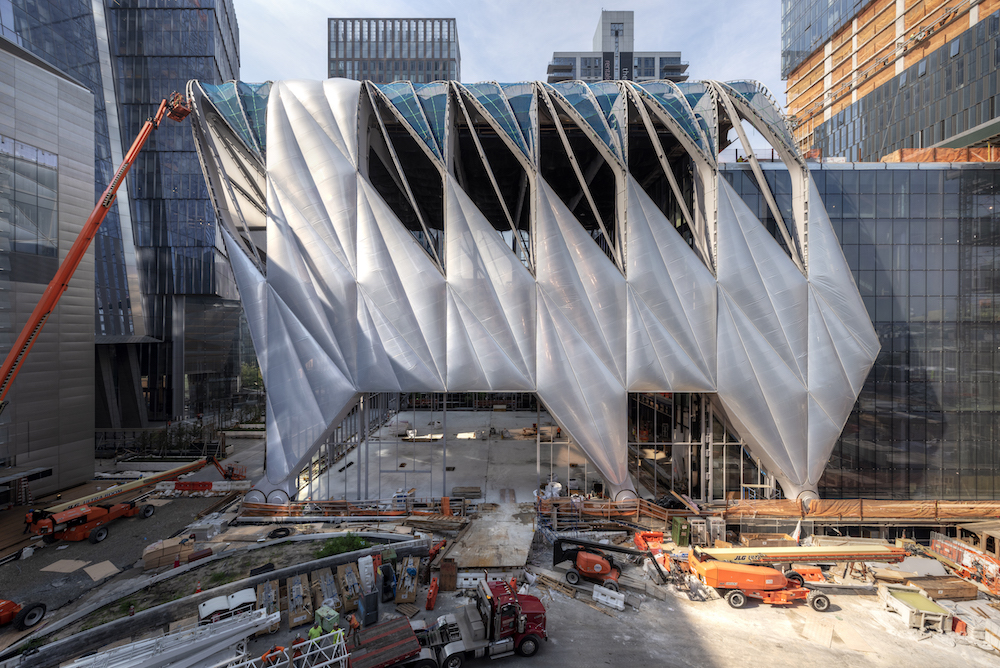
ETFE is a pliable and lightweight alternative to glazing. The Shed lies atop Hudson Yards’ foundational plate, which is composed of a vast network of trusses spanning old rail yards below, and the use of heavy, insulated glass units would potentially overload this nonadjustable structure. According to DS+R associate principal Charles Berman, ETFE was also chosen for its spanning capabilities and inherent flexibility. “ETFE can be fabricated into much larger, self-supporting, pneumatic cushions that allowed the facade to enclose the structural steel frame without intervening substructures of aluminum or steel,” Berman said. “ETFE’s flexibility permitted DS+R to address the dynamic deflections that The Bloomberg Building experiences when in motion without the complex moment allowances and expansion joinery that a glass and metal facade would require.”
Collaboration proved crucial to the project. DS+R, facade consultant and structural engineer Thornton Tomasetti, contractor Sciame, and fabricators were involved from the early design-assist phase. According to Thornton Tomasetti associate Alloy Kemp, the early stages of the design sought to push the limits of the ETFE panel size while meeting the daylighting and acoustical requirements of the performance space within. The structural steel frame is girded with a U-shaped upstand that is fastened at key points; fabricator Cimolai assembled each component in Pordenone, Italy, prior to shipment to New York. Once in place, the steel shell was outfitted with aluminum extrusions and plates, and then the ETFE panels were installed. Inflation tubing was set for each panel during the installation process.
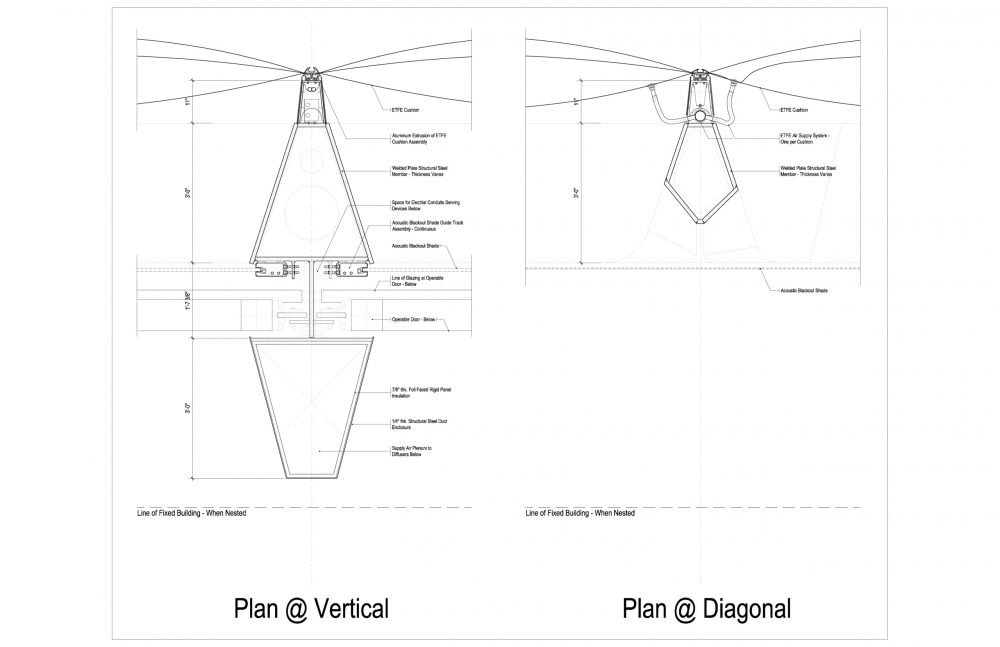
The material and location also presented unique challenges for the contractor. “ETFE must be installed in temperatures above 40 degrees Fahrenheit. Any colder and the material becomes brittle and will lack the pliability needed for installation,” said Sciame senior vice president Steven Colletta. “Getting the material to look right—it cannot be too tight or too slack—required a great deal of field adjustment and coordination to account for the anticipated movement of structural steel, all the more complicated because of Hudson River–borne winds.”