Garages are fairly ubiquitous across Florida—the state has one of the highest car ownership rates in the country—but in recent years, the local typology has received a bit of a revamp. Opened in February 2019, Sarasota’s St. Armands Circle Garage continues this trend with a spiraling stainless steel mesh skin. The $12 million project was designed by Sarasota-based Solstice Planning and Architecture and rises to a height of three stories to accommodate 480 spaces.
The facade is clad with a total of 520 spiraling panels, with the majority measuring 1-foot wide by 20-feet tall. Encompassing over 9,000 linear feet of mesh, the panels are held together by 250,000 individual welds completed by hand by manufacturer Cambridge Architectural’s fabrication team.
Located on Florida’s Gulf Coast, the project is prone to major hurricane winds during summer and fall. “In Sarasota we had to consider winds up to 50 percent higher than are common on most projects, so each of our system components required more custom design and manufacturing to account for extra wind load transfer,” said Cambridge Architectural business director David Zeitlin. “In addition, there needed to be close collaboration with the structural engineering team on an ongoing basis to ensure proper integration into the garage, and together that the project met industry standards.”
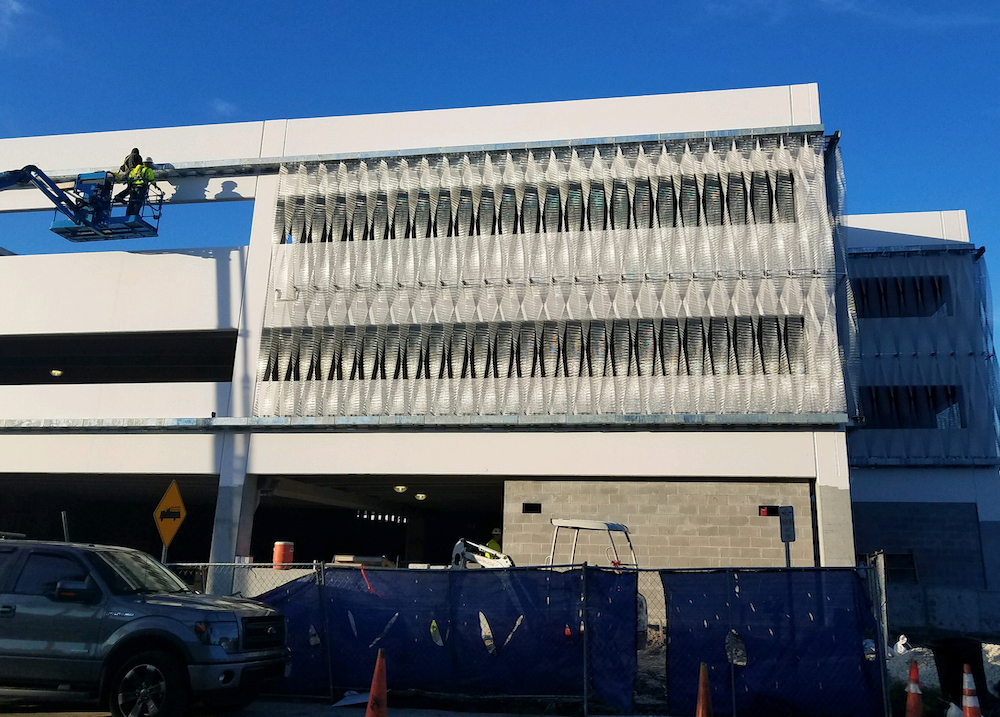
To achieve the spiraling character of the panel, Cambridge Architectural and the installer L&S Erectors collaborated closely. Firstly, the mesh was welded to a series of base plates at Cambridge’s manufacturing facility in Cambridge, Maryland. Once welded, the panels were shipped to the project site in Florida. As the concrete garage was poured, the construction team embedded mounting channels from the second to third stories. The plates at the end of each panel were then bolted to the channels and twisted into their distinctive shape on site.