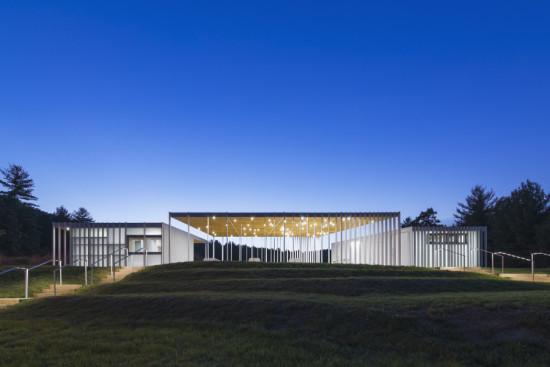
Virginia Tech students demonstrate a light touch with glass and steel pavilion.
The undergraduate architecture students enrolled in Virginia Tech‘s design/buildLAB begin each academic year with an ambitious goal: to bring a community service project from concept through completion by the end of the spring semester. In addition to the usual budget and time constraints, the 15 students taking part in the course during the 2013-2014 school year faced an additional challenge. Their project, a public pavilion for Clifton Forge Little League in the tiny hamlet of Sharon, Virginia, was entirely lacking in contextual cues. “It was interesting because our previous design-build projects have been downtown, with lots of context,” said Keith Zawistowski, who co-founded and co-directs design/buildLAB with his wife, Marie. “Instead, we had a pristine, grassy field with a view of the mountains. We joke that this is our first group of minimalists.” The students’ understated solution—three geometric volumes unified by the consistent use of a vertical sunscreen—turns the focus back to the pavilion‘s surroundings with a restrained material palette of concrete, glass, and steel.

Design/buildLAB assigned a separate structure to each element of the Sharon Fieldhouse program, nestling the open-air public pavilion between glass boxes containing the restrooms and concessions kitchen. Different roof heights distinguish the spaces, yet a common material vocabulary and their arrangement along a single horizontal axis allows them to be read as a single object. “The students describe the field house as a linear incision through the site,” said Zawistowski. “Basically it’s just light cut through the green landscape.”
Because Sharon Fieldhouse is intended for seasonal use, the students focused on maximizing environmental performance for the warmer months of the year. “Everything’s about cooling and ventilation,” said Zawistowski. A no-energy ceiling fan cools the kitchen, and tempered laminated white glass helps cut solar gain inside the enclosed areas. “The glass has a translucent quality, so that the spaces are bathed in even light, eliminating the need for electrical lights during the day,” explained Zawistowski.

- Facade Manufacturer
design/buildLAB - Architects
design/buildLAB - Facade Installer
design/buildLAB - Location
Sharon, VA - Date of Completion
2014 - System
laminated glass wind screens with custom-built steel sunshade - Products
BMG Metals structural steel, white laminated glass from AGC Glass
The external sunshade, comprising vertical steel plate elements painted white, serves both conceptual and practical ends. “The shade screen is about intimacy and privacy—not just under the open-air pavilion but in the enclosed spaces,” said Zawistowski. “The elements vary in density. They’re tighter together toward the more private parts of the building.” At the same time, larger gaps between the screen’s members on the east side of the pavilion welcome in the morning sun, while to the west the steel bars draw together to provide afternoon shade. The screen simultaneously functions as skin and structure. “In most cases, the sunshade is tacked on. In this case it’s part and parcel of the architecture,” observed Zawistowski. Wider steel bars take the weight of the building’s roof, and help conceal downspouts. “Everything is hidden there in the screen,” said Zawistowski. “We brought a new group of students to the field house and asked them if they could figure out how rainwater could get off the roof. They didn’t know.”
The students prefabricated portions of the pavilion at Virginia Tech’s Blacksburg campus, panelizing the screen members and roofing. “One thing that bothers us in design-build education is that multiple generations tend to work on one project,” said Zawistowski. “It’s important for us that the same group sees the implications of what they design, so we rely really heavily on prefabrication.” On campus, he added, students are able to take full advantage of the university’s resources. Once on site in Sharon, the students completed assembly in just a couple of weeks.
Given the fact that his students conceived of, fundraised for, programmed, planned, designed, and built Sharon Fieldhouse in less than ten months, it’s no surprise that Zawistowski refers to the supernatural when he talks about the project. But when he brings up hocus-pocus, it is as much about the pavilion’s aesthetic impression as it is about the speed with which it was brought into being. “We say that it’s put together with magic,” he mused. “All the connections are hidden—everything’s just light and shadow.”
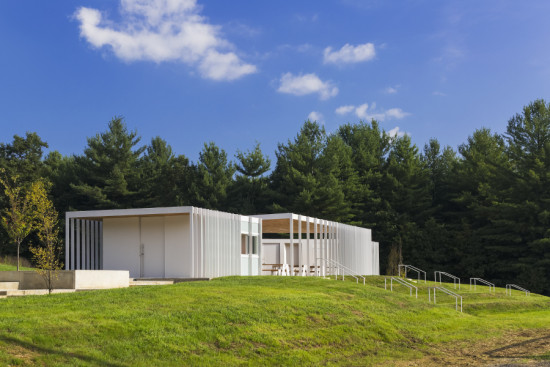